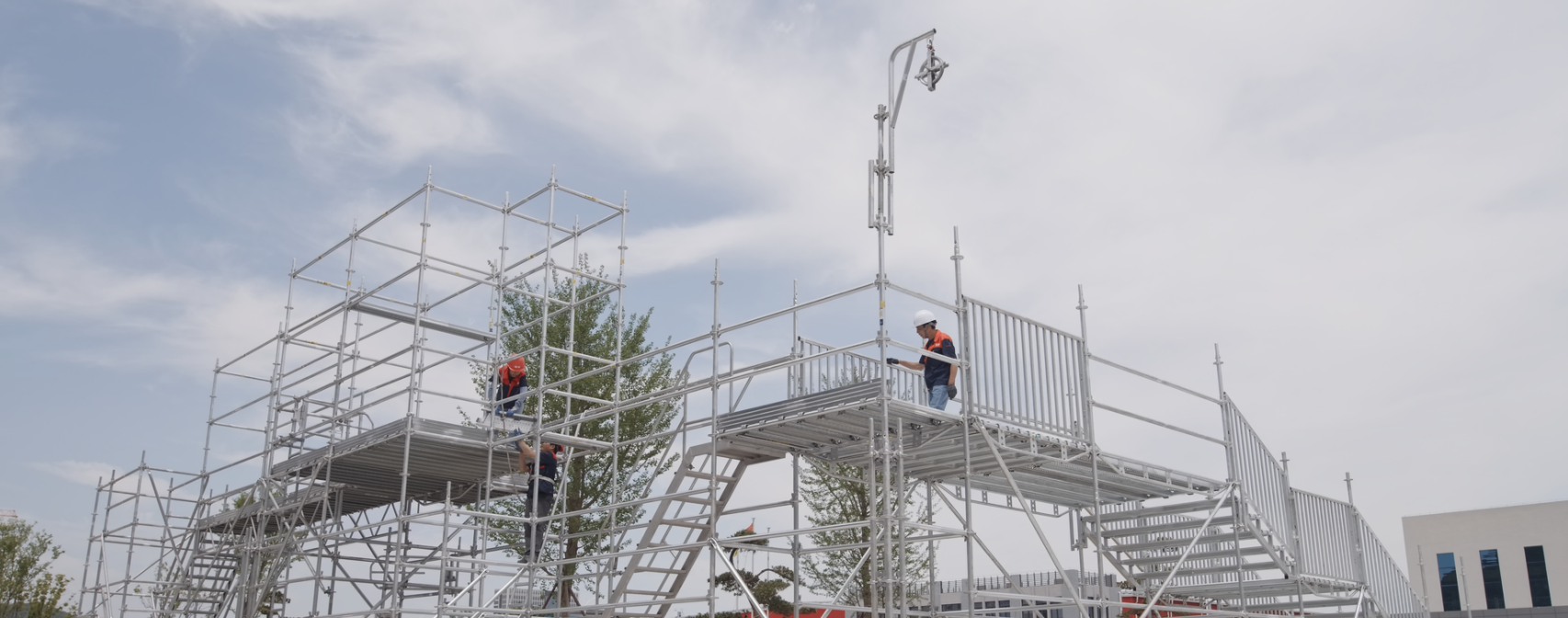
Why Large-Scale Construction Projects Prefer Ringlock Scaffolding: Benefits for Efficient and Safe Operations
Why Large-Scale Construction Projects Prefer Ringlock Scaffolding: Benefits for Efficient and Safe Operations
In recent years, an increasing number of large-scale infrastructure and industrial projects worldwide have adopted Ringlock scaffolding systems. Many governments actively encourage or even mandate the use of Ringlock scaffolds, particularly for complex, high-risk, and labor-intensive projects. Understanding the reasons behind this trend is crucial for contractors and procurement specialists aiming to ensure both safety and efficiency on site.
Stable and Robust Structural Framework
Ringlock scaffolding is engineered around a modular spatial truss system composed of vertical standards, horizontal ledgers, and diagonal braces. These components are interconnected through precision-cast or pressed steel rosettes welded firmly to the standards. The system employs wedge pins and connector plugs to lock ledgers and braces into place, forming a stable and rigid framework. This configuration offers superior load distribution and structural integrity, enabling rapid assembly with enhanced stability and high load-bearing capacity.
Reliable and Secure Connection Points
The design of the connection nodes is critical to scaffold safety. Ringlock scaffolds feature rosettes that provide multiple locking points for ledgers and braces. The ledger heads engage the rosette securely with wedge pins, creating a self-locking joint that effectively transfers loads from the horizontal components through the rosette to the vertical standards. The system's wall ties, braces, and suspension points are engineered to safely resist shear and tension forces, ensuring reliable support under dynamic working conditions.
High-Quality Materials with Advanced Hot-Dip Galvanization
All major load-bearing components, including vertical standards, ledgers, and diagonal braces, are manufactured to stringent quality standards. Typically available in two primary diameter classes (φ60 mm and φ48 mm), the standards offer impressive load capacities—up to 18 tons for φ60 and 12 tons for φ48 systems—providing scalable strength tailored to specific project demands. Each component undergoes hot-dip galvanization, delivering exceptional corrosion resistance that extends service life and maintains structural performance over time, even in harsh environmental conditions.
Enhanced Safety Through Self-Locking Mechanism
A defining feature of Ringlock scaffolding is its semi-circular concave ledger heads that, when hammered onto the rosette with wedge pins, create a robust bidirectional self-locking joint. This design ensures that the horizontal loads applied to the ledgers are efficiently transmitted through the rosette to the vertical standards and then directly downward to the foundation. This gravity-assisted locking mechanism greatly reduces the risk of accidental disassembly or component displacement, thereby enhancing on-site safety.
Durability and Resistance to Wear and Tear
Without reliance on traditional bolts, the Ringlock system reduces weak points susceptible to loosening or damage. Its components are designed to endure frequent assembly and dismantling cycles while maintaining performance. The robust construction allows the scaffolding to withstand impacts and corrosion, with typical service lifespans exceeding 10 to 15 years, making it a cost-effective investment for recurring projects.
Simplified Logistics and Storage
Ringlock scaffolding's modular simplicity — consisting solely of vertical standards, horizontal ledgers, and diagonal braces, all factory-fabricated without loose parts — facilitates streamlined storage, handling, and transportation. Standardized packaging ensures components remain organized and protected throughout the supply chain, reducing losses and damage.
Conclusion
The application of Ringlock scaffolding in large-scale, high-complexity projects is underpinned by its proven safety, reliability, and efficiency advantages. Understanding the mechanical principles and critical control points of load transfer and joint locking is essential for maximizing these benefits during construction.
As a dedicated Ringlock scaffolding manufacturer, HJ Scaffolding provides high-quality, factory-produced components designed to support your on-site systems. Whether you're an engineering contractor, rental company, or scaffolding solution provider, we can supply you with durable, compliant, and precision-made products to match your project requirements.
We don't offer scaffolding services — we power the companies that do.
Looking for reliable Ringlock scaffold components? Let's connect.
Web:www.hj-scaffolding.com
E-mail:lynn.li@hj-scaffolding.com
WhatsApp: +86 15058750031